SPECIAL COATINGS
Lunac: the rare combination of ultimate
hardness and corrosion resistance
Almost no construction metal is capable to combine ultimate corrosion resistance with high hardness and tensile strength. As a rule the elevated noble (such as copper) or noble metals (such as gold, except the precious noble metals Ruthenium* and Iridium) are too soft to withstand high (adhesive) wear loads. In the case of alloys, high tensile corrosion resistant alloys such as martensitic SAE 430 stainless steel offer lower corrosion resistance than the weaker austenitic stainless steels (such as 316L). In almost all adhesive-wear systems at least one surface needs to be hard. Consequently, coatings should offer the solution, but almost all coatings which are hard as well as corrosion resistant suffer from cracking or porosity problems. We finally solved this wide spread limitation successfully after a long research program with the hard, corrosion resistant and crack-free Lunac coatings. The major mechanism is; Lunac coatings are highly homogeneous.
Corrosion testing:
In the diagrams below you can find corrosion levels of various materials in a strong
halogen HCl/HF acid mixture (representative for many harsh corrosive conditions).
Note, strong oxidizing agents such as HNO3 can often practice a protective effect
on chromium or high chromium containing steel.
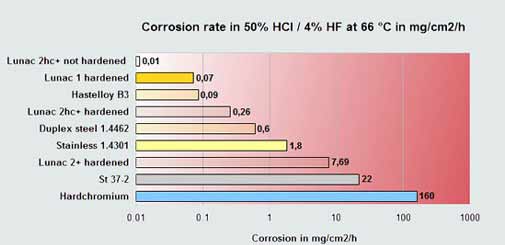
Diagram 1
In corrosion perspective this corrosion testing
diagram displays two different metal types :
|
Metals with improved resistance to oxidizing environment such as HNO3 or H2O2. These metals can benefit from the metal oxide augmenting action of these chemicals, provided that the metal oxide layer is dense and offers good bonding. Chromium, Titanium, Stainless steel or Aluminum are good examples of these metals or alloys. Lunac coatings, copper or steel do not comply with this mechanism and are less chemically resistant in these chemicals.
|
Metals with improved resistance to non-oxidizing acidic environments such as HCl, H2SO4, HF, acetic acid, citric acid etc. Therefore, the majority of acids. These metals and alloys mostly benefit from their higher electro-potential, so the more noble base metals and noble metals. Copper, Tin, Nickel, Lunac 1 and 2+ or silver are good examples of these metals or alloys. The metals as mentioned at 1. show visa versa no good corrosion resistance to these acids.
|
Corrosion mechanisms:
Both hard and corrosion resistant Lunac 1 and 2+ industrial coatings stay fully crack- and pore-free in the case the substrate is 1- free of serious defects and 2- ground smoothly in advance (Rz< 2.0 µm / 0.079 mil). The latest introduced technical hard nickel intermediate coating offers ultimate repair capability of surface micro-defects. Good corrosion resistance can not only be obtained by higher electro-potentials or dense oxide layers, but also by means of stress-free lattices, or even better, amorphous structures. In this way a material or coating with a lower electro-potential but crystal free structure can often deliver the same corrosion resistance as a more noble crystalline material. The additional advantage of such system is less galvanic corrosive activity and substantial cost savings. There are Lunac versions with no crystalline structure and small potential differences with steel. Moreover, hard coatings such as the Lunac systems which contains crack inhibiting compressive stresses are very rare. The latest Lunac 2+ duplex version even resists corrosion after plastic deformations because of the ductility of the intermediate technical hard nickel and the superb bond quality.
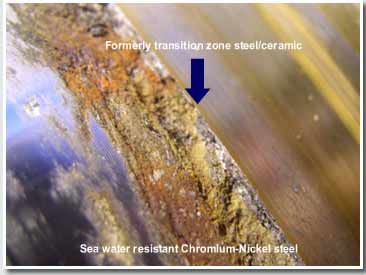
Figure 1: The consequences of porosity in a HVOF ceramic coating on 1.4462 (duplex steel) with high pitting and inter granular corrosion resistance, became visible not before the ceramic coating was removed from this prop shaft. The corrosion beneath the coating reached out over +/- 4 mm depth. Most likely the steel suffered from this corrosion because of a devastating salt concentration effect and high local temperatures, despite the application of the highly sea water resistant Chromium-Nickel-Molybdenum steel. Lunac coatings proved to inhibit this effect due to the dense structure, good heat conductance and their inertness.
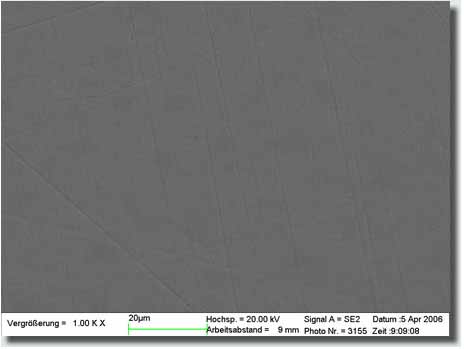
Figure 2: Lunac 1 (displayed left) and Lunac 2+ coatings contain compressive stresses and will consequently inhibit micro-crack formation during hardening. Hard chromium coatings (displayed below) develop micro-cracks after being deposited, due to tensile stresses. These micro-cracks generally highly compromise the corrosion resistance.
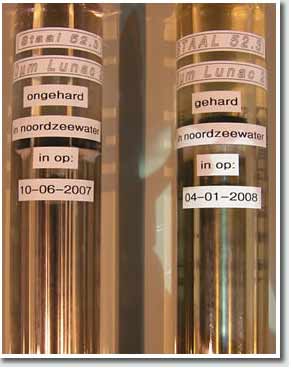
Figure 3: Submersed sea water exposure test of smoothly ground St 52.3 rods, plated with 50 µm Lunac 2+, not hardened (left) and hardened (right). Start of tests: 06/10/07 and 01/04/08. The corrosion resistance of the hardened Lunac 2+ version is reduced, but still good enough to perform well in sea water. This offers hardened Lunac 2+ the unique feature of being very hard (HRc 72/Hv 2200) as well as corrosion resistant as well as crack free. For these characteristics Lunac 2+(duplex) is very often applied to hydraulics and axles in marine environments. The surface of Lunac 2+ coatings can slowly tarnish when not used in the same way copper does (the surface of the rod in the right bottle turned a bit gray. After a few days the slightest pore would have commenced the production of massive orange 'rust clouds'. Date of photo: December the 29th , 2011.
Coated carbon steel corrosion after local coating
destruction or in coating/substrate transition zones
In reality coating damage due to accidents is likely to happen or coating / substrate transitions are present (end of coating). In a corrosive environment almost all protective noble (metallic) coatings will accelerate the steel (galvanic) substrate corrosion in these damaged spots. As a reference, passive organic coatings (paintings) show a neutral behavior. Lunac 2+ duplex coatings are optimized to come as close as possible to these passive coatings and do not show significant sub-surface corrosion.
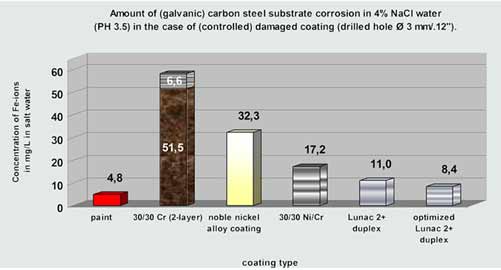
Diagram 2: Corrosion testing in Ø 3 mm / .12" (800 µm / 0.03" deep) 'through coating' holes at 40 °C / 104 °F.
Note: the 30/30 µm chromium coating developed an additional, hardly dissolvable
oxide layer (visualized in brown) with major sub surface spreading characteristics.

Left: 30 µm chromium on carbon steel coating displays major sub (coating) surface corrosion spreading after 37° C / 99°F , 400 hours 4% salt spray corrosion testing.
Middle: 30/30 µm duplex chromium on carbon steel with a 3 mm/.12" hole (originally). The sub (coating) surface corrosion spreading (widening of the 3 mm hole) after 8 days acidic salt water corrosion testing is clearly visible.
Right: 110 µm Lunac 2+ duplex on carbon steel with a 3 mm/.12" hole. No sub (coating) surface corrosion can be observed after 8 days acidic salt water corrosion testing. The (in depth) galvanic corrosion is one of the lowest achievable in the category 'corrosion resistant coatings with noble behaviour'.
Neutral salt spray tests and the influence of intermediate ductile nickel layers
in the case of moderate indentations (depth, a few tenth of a mm at Ø 8 mm )
Corrosion after indentation
Although most Nickel-chromium coatings on carbon steel perform well within 1000 hours of Neutral Salt Spray testing and are capable the deal with small accidents as well, they generally start developing rust spots after the 1000 hours period. All tested hard and brittle mono-layer coatings show up corrosion along the micro-cracked edges (picture 6 and 7). Only the Lunac 2+ duplex coating proved to be the very long lasting hard corrosion-protective coating (2400 hours NSS test already proven) that is capable to deal with indentations as well.
Lunac 2+ Grayish appearance
- The grayish appearance of the Lunac 2+ surface after prolonged water contact is caused by the development of a +/- 0.2 µm / 0.0079 mil stable conversion layer.
Comparison HVOF ceramic, hard chromium and Lunac 2+
- In contrast to HVOF ceramic duplex coatings, Lunac 2+ duplex does never peel and Ni-Cr does mostly not peel on loading.
In perspective of hardness and scratch resistance, Lunac 2+ should be compared with HVOF ceramic coatings.
Lunac 2+ duplex has since the 26th of September 2011
been qualified to offer long lasting corrosion protection,
according to NBD 10300 (Rijkswaterstaat). This test is
based on the EPQ test as described in ASTM G59-97
(2003) and ASTM G61-86 (2003).